Шлифовальные станки для обработки древесины. Часть 2
Шлифовальные станки для обработки древесины (часть 2)
Статья опубликована в специализированном журнале "Шпиндель", № 3 2006 год.
В предыдущей статье мы рассмотрели основные положения процесса шлифования цревесины технологическое назначение и конструкции различных видов узколенточных шлифовальных :танков. В данной статье мы ознакомимся с наиболее интересными и перспективными по своим возможно :тям и конструкциям широколенточными шлифовальными станками.
Большее распространение, в сравнении с другими видами шлифовального оборудования, широколенточные станки получили из-за ряда преимуществ.
К ним относятся: повышенная производитеотность; более высокая удельная мощность шлифования; высокие точность и качество обработки; высокая стойкость и работоспособность ленты вследствие значительной ее длины, лучшая очистка от отходов обработки; удобство встраивания в поточные и автоматические линии и ряд других. Так, например, при ширине шлифования 600-900 мм производительность таких станков на порядок выше, чем узколенточных, при выполнении одинаковых технологических операций. Если узколенточные станки применяются, в основном, на небольших предприятиях и специфических технологических операциях, то широколенточные станки целесообразно использовать на достаточно крупных предприятиях в серийном и крупносерийном производстве деталей при обеспечении высокой стабильности размеров и качественных параметров обработки.
К недостаткам широколенточных станков следует отнести достаточно высокие затраты на их эксплуатацию за счет заметной стоимости самой шлифовальной ленты, а также ее склейки и подготовки к работе, которые обычно выполняются централизованно на специализированных предприятиях.
В статье кратко описаны цилиндровые и дисковые шлифовальные станки, которые пусть и все реже, но еще встречаются на производстве.
Широколенточные шлифовальные станки
Широколенточные шлифовальные станки предназначены для обработки пластей щитовых и плитных заготовок и деталей на их основе. Формально к широколенточным станкам относят станки с шириной ленты более 300 мм. Однако в деревообработке наибольшее распространение получили станки с шириной ленты 650-1300 мм, хотя ее максимальная ширина может достигать 3600 мм.
Другими признаками наряду с шириной ленты, характеризующими принадлежность станка к группе широколенточных, являются: направление подачи обрабатываемых заготовок, как правило, встречно направлению шлифования; шлифование детали осуществляется по всей ее ширине; подача детали механизирована; станок снабжен устройствами обеспечения устойчивого движения шлифовальной ленты.
Конструкции широколенточных станков весьма разнообразны, в первую очередь в зависимости от технологического назначения.
По расположению шлифовальных агрегатов относительно базового стола различают станки с их верхним, нижним и двухсторонним расположением. По виду контактного взаимодействия шлифовальной ленты с обрабатываемой заготовкой различают станки с вальцовым контактом, утюжковым контактом и комбинированные. В зависимости от числа установленных на станке шлифовальных агрегатов существуют станки одно-, двух- и трехленточные.
По технологическому назначению станки с широкой лентой классифицируются следующим образом:
- шлифовальные станки с вальцовым контактом служат в основном для калибрования плит и щитов различной структуры в размер по толщине и выравнивания их поверхностей;
- станки с утюжковым контактом предназначены для выглаживания облицованных шпоном или покрытых грунтами либо лакокрасочными материалами поверхностей с частичным их выравниванием;
- комбинированные станки позволяют производить за один проход все перечисленные операции либо какие-то две из них - калибрование, выравнивание и выглаживание.
Калибровальные станки предназначены для обработки клееных щитов, ДСтП, ДВП и других щитовых и плитных деталей из древесины и композиционных материалов на ее основе в заданный размер по толщине при обеспечении заданной шероховатости.
На рисунке 1 представлены технологические схемы таких станков.
Рис. 1. Принципиальные схемы
широколенточных шлифовальных станков
для калибрования плит и щитов
Основным признаком калибровальных станков является постоянный, неизменный в процессе работы станка зазор между базирующими и режущими органами. Так, для станков, работающих по схемам а и г, таким зазором является расстояние между поверхностями контактного вальца 1 со шлифовальной лентой 2 и контактного ролика 6; для двухсторонних станков, работающих по схеме б, - расстояние между поверхностями контактных вальцов верхнего и нижнего шлифовальных агрегатов. При этом для каждого агрегата противоположный контактный валец является базирующим. Для станков, выполненных по схеме в, поддерживается постоянное расстояние между поверхностями контактного вальца 1 со шлифовальной лентой и подающего конвейера 8.
При шлифовании на одноагрегатных калибровальных станках припуск снимается с одной стороны детали, и она обрабатывается, как правило, в два прохода - сначала с верхней, а затем и с нижней пласти. При таком способе калибрования неизбежно несимметричное распределение припуска между пластями - основной припуск сошлифовывается на первом проходе. Поскольку композиционные древесные материалы имеют анизотропное строение (наружные слои в первую очередь у прессованных плитных материалов более плотные, чем внутренние), снятие несимметричных припусков с верхней и нижней пластей приводит к короблению деталей после калибрования. Этот же недостаток присущ и двухсторонним станкам с разнесенными по зонам обработки шлифовальными агрегатами (схема г), если они не оснащены центрирующими устройствами, симметрично распределяющими припуск между верхним и нижним калибровальными агрегатами. Наибольшее распространение получили станки с противоположным расположением калибровальных агрегатов в одной вертикальной плоскости (схема б). При шлифовании на таком станке осуществляется самоцентрирование калибруемых деталей за счет уравновешивания сил отжима, т.е. вертикальных составляющих сил резания, возникающих при
шлифовании. При одинаковой структуре и плотности верхнего и нижнего слоев обрабатываемого материала (например, ДСтП) будет обеспечено снятие равных припусков обоими калибровальными агрегатами. Подобные станки могут иметь до четырех и более спаренных калибровальных агрегатов с разной зернистостью шлифовальной ленты и обеспечивать разнотолщинность плиты до +/-0,1 мм при ширине плит до 3200 мм. Для повышения точности обработки некоторые фирмы выпускают калибровальные станки с литой каменной (минеральной) станиной, обладающей высокой термостабильностью.
Такие станки относятся к специальному оборудованию, и наибольшее распространение получили в производстве ДСтП.
В настоящее время получают распространение калибровальные станки, в которых, по аналогии с рейсмусовыми станками, роль калибрующего агрегата выполняет ножевой вал.
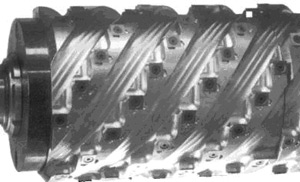
На ножевом валу (рис. 2) по винтовой линии крепятся резцы - поворотные неперетачиваемые твердосплавные пластинки с большим периодом стойкости, число которых может достигать четырех-шести сотен штук.
Операция калибрования может также выполняться на цилиндровых станках, где режущий инструмент представляет собой протяженный абразивный цилиндр из зерен карбида кремния на эпоксидной связке. Этот способ калибрования обеспечивает рост производительности в сравнении с ленточным практически в два раза за счет высокой стойкости шлифовального цилиндра при точности калибрования до +/- 0,07мм. Однако такие цилиндры достаточно дороги, требуют тщательной динамической балансировки и правки.
Широколенточные станки для выравнивания и чистовой обработки служат для устранения местных неровностей с обрабатываемой поверхности (до 300 мм по поверхности и до 0,2-0,4 мм по высоте) и снижения ее шероховатости.
Однако коробление и крылова-тость деталей, достигающие 1 мм/м, значения которых могут превышать толщину наклеенного облицовочного шпона, не устраняются после выравнивания. Для исключения прошлифовок при обработке деталей с допустимой неплоскостностью, такие детали необходимо базировать обрабатываемой поверхностью по плоским или цилиндрическим специальным опорным устройствам станка, расположенным как можно ближе к шлифовальной ленте. Благодаря упругому покрытию контактного вальца или прижимного утюжка шлифовальная лента повторяет неплоскостность щита, копируя, его поверхность.
Технологические схемы наиболее распространенных станков для выравнивания и чистовой обработки представлены на рисунке 3. В большинстве своем это станки с верхним расположением шлифовальных агрегатов, поскольку такая компоновка станка гораздо удобнее в обслуживании и эксплуатации, поскольку оператор имеет возможность легко контролировать качество обработки визуально, так как обработанная пласть детали обращена вверх.
На станках с вальцовым контактом (а, б) подача заготовок, обрабатываемых шлифовальным агрегатом 1 с контактным вальцом 2, осуществляется либо ленточным конвейером б, либо приводными вальцами 9 и контрроликом 8. Базируют заготовку 5 обрабатываемой пластью по опорным балкам 3 и роликам 4. Для компенсации разнотолщинности стол 7 подающего конвейера выполнен подпружиненным, также как и подающие вальцы и контрролик во второй схеме. Резиновая лента подающего конвейера выполняется с протекторным рисунком, внутри впадин которого имеются отверстия для соединения с вакуумной системой станка, обеспечивающей за счет разрежения воздуха равномерный прижим обрабатываемого щита к столу.
Конструктивно большинство современных широколенточных станков выполнено по модульному принципу, позволяя на единой конструктивной базе типовых узлов создавать шлифовальные станки различного технологического назначения.
Базой таких станков чаще всего является стальная сварная станина коробчатой формы, прошедшая термообработку и искусственное старение. Внутри станины монтируются приводы шлифовальных агрегатов, вакуумная система, обеспечивающая прижим обрабатываемой заготовки к столу, и привод перемещения стола по высоте. На внутренних боковых стенках станины крепятся направляющие, по которым стол перемещается по высоте при настройке на толщину обрабатываемой детали. Обычно перемещение стола осуществляется с помощью четырех винтовых синхронизированных пар от электродвигателя через червячный редуктор.
Подача обрабатываемой заготовки по столу современных станков обеспечивается конвейером с перфорированной протекторной лентой, выполняемой из вакуумной резины. Конвейер приводится в движение от собственного электродвигателя с редуктором, закрепленным на раме стола. Обычно используется двухско-ростной электродвигатель, обеспечивающий две скорости подачи, либо, как опция, электродвигатель с частотным управлением, позволяющий плавно изменять подачу в широком диапазоне скоростей.
В некоторых конструкциях станков конвейерная лента осциллируете амплитудой до 10 мм вместе с обрабатываемой деталью относительно стола, что также способствует повышению качества шлифования.
Прижим заготовки к резиновому конвейеру обеспечивается атмосферным давлением при включении вакуумного насоса, расположенного внутри станины и создающего разрежение под заготовкой через отверстия в столе и впадинах протекторной резиновой ленты конвейера. Такая система прижима налагает определенные ограничения на минимальные размеры обрабатываемой детали, поскольку усилие прижима зависит от площади ее базовой поверхности. Эти ограничения, изложенные в паспорте станка, необходимо выполнять для каждого типа станка для надежного закрепления детали на конвейере и исключения возможности выброса ее из станка в процессе обработки, поскольку силы резания при шлифовании зависят, в том числе и от типа шлифовального агрегата и их количества на станке.
На верхней поверхности станины предусмотрены крепежные элементы для установки шлифовальных агрегатов типовых конструкций различного технологического назначения. Снаружи шлифовальные агрегаты закрываются защитными кожухами, повышающими безопасность работы, снижающими шум и запыленность, а также обеспечивающими эстетическую законченность композиционного построения станка. Под кожухами крепятся и вспомогательные устройства - механизмы осцилляции, пневматические системы натяжения и обдува ленты, регулирования съема припуска, удаления шлифовальной пыли и т.д.
Следует сразу отметить, что широколенточные шлифовальные станки напоминают в большой степени по конструкции и технологическому назначению рейсмусовые станки, служащие для калибрования в размер деталей по толщине. Общим у этих двух групп станков является то, что высота базовой поверхности стола (подающего конвейера) изменяется относительно уровня пола в зависимости от толщины обрабатываемой детали, что иногда вызывает определенные сложности при их встраивании в линии деревообрабатывающего оборудования.
Основным механизмом широколенточного шлифовального станка является шлифовальный агрегат. Назначение станка (калибрование, выравнивание или чистовая обработка) определяет конструкцию агрегата, его параметры и размеры. Шлифовальный агрегат обычно выполняется в виде самостоятельного модуля и его основой, как правило, является корпус, установленный в несущих кронштейнах на станине станка. В подшипниковых опорах корпуса устанавливаются чаще всего два или три вальца с натянутой на них широкой шлифовальной лентой. Для замены отработавшей ленты один из несущих кронштейнов выполняется съемным.
Количество, расположение и функциональное назначение вальцов в шлифовальных агрегатах может быть различным. Возможное наименьшее количество вальцов агрегата - два (рис. 3, а).
Рис. 3. Принципиальные схемы
широколенточных шлифовальных станков
для выравнивания и чистовой обработки деталей
В таком агрегате нижний валец - контактный -обычно приводной и одновременно прижимной, поскольку прижимает ленту к обрабатываемой поверхности. Верхний валец является натяжным, с его же помощью обеспечивается осцилляция ленты, т.е. ее перемещение относительно заготовки с заданной амплитудой в направлении, нормальном вектору скорости подачи для создания условий лучшего перерезания волокон древесины, снижения засаливания шлифовальной ленты и устранения продольных царапин на обработанной поверхности.
Станки с вальцовым контактом обеспечивают удовлетворительное качество выравнивания поверхности детали, однако не позволяют добиться ее высокой чистоты. Заданная шероховатость достигается при съеме с поверхности незначительного по толщине равномерного слоя древесины или лакокрасочного материала, что требует обеспечения одинакового давления по всей площади контакта шлифовальной ленты с заготовкой.
Для достижения этой цели станок оснащается шлифовальными агрегатами стремя вальцами и эластичным поперечным утюжком. Схема такого станка (рис. 3, в) напоминает схему станка, выполненного по схеме (а), аналогичной описанной в предыдущей статье для узколенточных станков. Однако прижим шлифовальной ленты к заготовке осуществляется не контактным вальцом, а эластичной контактной балкой 10, расположенной между двумя горизонтальными вальцами меньшего диаметра.
Еще больший эффект достигается установкой в одном шлифовальном агрегате 14 последовательно двух контактных балок - система «дуплекс» (схема е). При этом давление в балках регулируется микропроцессором независимо друг от друга - во второй контактной балке оно задается более низким, чем в первой, за счет чего толщина снимаемого слоя и шероховатость уменьшаются после зоны прижима ленты каждой из балок при одной и той же зернистости используемой шлифовальной ленты. Качество обработки шлифованной поверхности с использованием такой балки фактически соответствует обработке двумя шлифовальными агрегатами. Применение балки данной конструкции позволяет значительно снизить энергозатраты на шлифование, расход воздуха, уменьшить габариты станка.
Обычно утюжки прижимной балки дискретно перемещаются в вертикальной плоскости параллельно плоскости стола. Выпускаются станки с балками, в которых
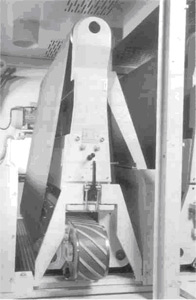
собственно прижимные утюжки устанавливаются на шаровых опорах, что позволяет им разворачиваться в горизонтальной плоскости, приспосабливаясь к сложной поверхности детали. В первую очередь это важно при обработке поверхности вблизи кромки детали для исключения прошлифовок шпона или лака.
В некоторых конструкциях широколенточных станков с целью повышения качества шлифуемой поверхности шлифовальный агрегат выполняют с модифицированным утюжко-вым контактом, когда внутри широкого утюжка движется поперечная протекторная лента с графитовыми пластинами, расположенная между пневматическим утюжком и шлифовальной лентой.
За счет постоянного перемещения графитовых пластин протекторной ленты обновляются рабочие участки шлифовальной ленты, на которые передается давление от пневматического утюжка. Это значительно снижает вероятность проявления на шлифованной поверхности следов осцилляции -рисок, характерных при обработке поверхности обычными агрегатами.
Обеспечение качественного выравнивания поверхности при обеспечении высокой производительности достигается дублированием шлифовальных агрегатов с вальцовым контактом, обрабатывающих последовательно деталь двумя и более агрегатами с лентой разной зернистости.
Причем первый шлифовальный агрегат, как правило, снабжен жестким стальным вальцом, а второй - обрезиненным, либо обрезинен-ными вальцами разной твердости. Каждый последующий агрегат снимает меньший припуск, что позволяет производить обработку более производительно, экономически эффективно при высоком качестве шлифования. Существуют станки, в которых операции выравнивания и выглаживания осуществляются одним комбинированным шлифовальным агрегатом, объединяющим контактный валец и прижимной утюжок.
Установив на станке последовательно два (или более) шлифовальных агрегата, первый из которых - с вальцовым, а второй - с утюжковым или вальцово-утюжковым контактом - получаем комбинированный широколенточный станок, позволяющий за один проход как выравнивать, так и выглаживать поверхность детали.
К группе комбинированных станков относятся и станки, у которых передним шлифовальным агрегатом является агрегат с узкой поперечной лентой, осуществляющий предварительное шлифование поверхностей щитов.
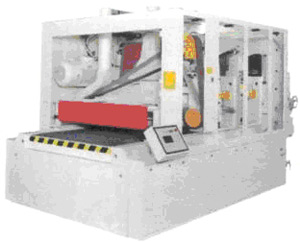
При этом на станке осуществляется так называемое перекрестное шлифование. Применение широкой ленты при наличии на поверхности щита продольных следов клеерасплава, склеивающей полосы шпона бумаги или синтетической нити приводит к появлению местного засаливания шлифовальной узкой ленты - на ней образуется засорившаяся кольцевая дорожка, приводящая к непрошлифовкам поверхности детали. Дорогую широкую ленту приходится выбрасывать. Узкая поперечная шлифовальная лента намного дешевле, а шлифует более равномерно, независимо от разности плотности зон ранней и поздней древесины. Однако основным является то, что при перекрестном шлифовании волокна не заглаживаются, не втираются в поверхность древесины, а именно перерезаются, что исключает в последующем поднятие ворса и позволяет наносить тонкие слои современных экологически чистых водорастворимых лакокрасочных материалов. Для этой же цели в некоторых станках устанавливаются последовательно два поперечных шлифовальных агрегата, причем в этих агрегатах направление движения шлифовальных лент встречное.
В некоторых комбинированных станках узколенточный шлифовальный агрегат разворачивают под углом 85 - 87 градусов к вектору подачи, что позволяет более эффективно бороться с таким дефектом, как вол-нообразность (специфическая рябь) на отшлифованной поверхности в первую очередь при калибровании плит на широколенточных станках.
При получении финишной поверхности под нанесение лакокрасочных материалов (в особенности изделий рамочной конструкции) используются комбинированные шлифовальные станки, на станине которых вслед за шлифовальным агрегатом с утюжковым прижимом устанавливаются один или два виброшлифовальных агрегата с широкими утюжками.
Эти агрегаты осуществляют двойное круговое движение: круговой прижим утюжка совершает вращательное движение с малой амплитудой и небольшим радиусом покрытия поверхности, но большой частотой, а сам утюжок, вибрируя в той же горизонтальной плоскости - круговое движение с большой амплитудой и большой площадью покрытия, но меньшей частотой. В результате движение шлифовальной ленты такого агрегата относительно детали происходит по сложной замкнутой спирали - гипоциклоиде, напоминающей движения опытного рабочего при шлифовании вручную или на станке с узким утюжком.
Виброшлифовальные агрегаты могут устанавливаться и на отдельной станине для встраивания в линии по финишному шлифованию изделий.
Ряд станков, как опцией, могут комплектоваться дополнительным цилиндром из нетканого абразивного мелкозернистого материала типа «скотч-брайт», позволяющего производить тонкое шлифование поверхностей, в том числе и после нанесения лакокрасочных покрытий.
Существуют комбинированные трехсторонние шлифовальные станки, в которых помимо шлифования пласти с помощью широколенточного агрегата осуществляется также и шлифование боковых продольных кромок щитов лепестковыми абразивными инструментами, установленными на шпинделях по бокам стола по аналогии с четырехсторон- ними продольно-фрезерными станками.
В настоящее время в мебельной промышленности достаточно широкое распространение получили клееные деревянные щиты. Для шлифования таких щитов используются комбинированные широколенточные станки, в которых для ликвидации разнотолщинности при склейке брусков и потеков полимеризовав-шегося клея на поверхности щита калибрование осуществляет ножевой вал, о котором был разговор выше, а выравнивание и выглаживание - агрегаты с контактными вальцами и утюжками.
Цилиндровые и дисковые
Цилиндровыми называют шлифовальные станки, у которых шлифовальная лента закреплена на образующей поверхности цилиндров. На станках этого типа выполняют операции калибрования, чистового шлифования щитовых деталей, а также снятия провесов после сборки столярно-строительных изделий.
Диаметр шлифовального цилиндра таких станков сравнительно невелик (280 - 350 мм), поэтому при работе на частоте вращения 1500 об/мин шлифовальная лента быстро засаливается. При этом сам цилиндр нагревается до достаточно высокой температуры, поскольку на его поверхности нанесен слой эластичного материала (фетра или войлока), служащий прокладкой между^шлифовальной лентой и стальным цилиндром, что не способствует ее охлаждению.
На рис. 8 представлены принципиальные схемы многоцилиндровых станков. Как правило, станки с нижним расположением цилиндров и станки для двухстороннего шлифования снабжены вальцовой подачей, а станки с верхним расположением цилиндров - конвейерной (чаще - ленточным конвейером по пневматически подпружиненному столу).
Рис. 8. Принципиальные схемы
цилиндровых шлифовальных станков
Примером станка с нижним расположением шлифовальных цилиндров может являться станок ШлЗЦВ19 (Шл - шлифовальный, 3 Ц - с тремя цилиндрами, В - с вальцовой подачей заготовки, 19 - с шириной шлифования 1900 мм), иногда еще встречающийся на отечественных деревообрабатывающих предприятиях.
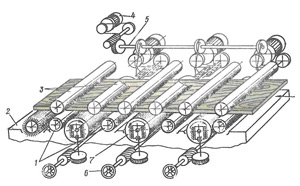
В этом станке заготовку базируют по неподвижному столу 2, в пазах которого установлены нижние приводные вальцы 1, осуществляющие подачу заготовки. Величину подъема вальцов над уровнем стола регулируют в зависимости от вида заготовки. Прижим заготовки к шлифовальным цилиндрам обеспечивают неприводными контрвальцами 3, расположенными в одних вертикальных плоскостях со шлифовальными цилиндрами 7. Каждый цилиндр имеет осциллирующее движение с амплитудой до 10 мм, создаваемое индивидуальным эксцентриковым механизмом с частотой 100 Гц. Он приводится в движение от электродвигателя 4 через общий вал 5, червячную и ременную передачи. Также каждый шлифовальный цилиндр снабжен механизмом для настройки по высоте на толщину снимаемого слоя, регулируемого маховиком б. Вальцы 3 установлены на единой раме, которую можно приподнять для обеспечения свободного доступа к цилиндрам при замене износившейся шлифовальной ленты. Очистка поверхности детали от шлифовальной пыли осуществляется щеточным агрегатом 5.
Длина шлифовального цилиндра достигает 2200 мм, поэтому его приходится тщательно балансировать статически и динамически. В большинстве конструкций цилиндров предусмотрены встроенные соответствующие балансировочные устройства. Абразивная лента в таких станках наматывается на цилиндр по винтовой линии. Усилие натяжения ленты и его равномерность обеспечиваются натяжным устройством. Как правило, передний цилиндр имеет встречное вращение, а два смежных цилиндра вращаются навстречу друг другу.
Достичь высокого качества обработки на станках цилиндрового типа не представляется возможным, поэтому в последнее время они в значительной степени вытеснены широколенточными станками.
В деревообработке для калибрования в первую очередь ДСтП появились станки, использующие в качестве режущего инструмента полый цилиндр из абразивных зерен на эпоксидной связке, насаживаемый на шпиндель станка, о чем говорилось выше.
Дисковые шлифовальные станки предназначены для шлифования по плоскости различных деревянных деталей небольших габаритов, ящичных конструкций и т.п. Механизмом резания этих станков является диск, установленный на валу электродвигателя (или два диска, когда используется электродвигатель с двухсторонним выходом вала), на плоской поверхности которого через фетровую прокладку обечайкой крепится шлифовальная лента в форме круга.
Наибольшее распространение получили станки с расположением диска в вертикальной плоскости. Данные станки относятся к разряду универсальных и в большинстве моделей дополнительно снабжаются вертикальным осциллирующим шлифовальным цилиндром - бобиной, позволяющей расширить технологические возможности станка за счет обработки как выпуклых, так и вогнутых деталей.
Примером такого станка является станок ШлДБ-б (Шл - шлифовальный, Д - дисковый, Б - с бобиной, б - шестая модификация), показанный на рисунке.
Комбинированный шлифовальный станок
с двумя дисками и бобиной ШлДБ-6
На станине 1 установлен электродвигатель 5 с двусторонним выходом вала. На концах валов закреплены шлифовальные диски 3 и б, имеющие диаметр 750 мм. Бобина
8, диаметром 90 или 120 мм при длине 210 мм, приводится во вращение от собственного двигателя, установленного внутри станины на кронштейне 10. Бобина, как правило, осуществляет еще и осциллирующее движение. Столы 2 и 7 перед шлифовальным диском могут наклоняться, позволяя обрабатывать базируемые по линейкам 4 детали под углом от - 15 до +45 градусов, а на столе 9 перед бобиной - +/- 30 градусов. Частота вращения диска сравнительно невысока - 750 об/мин, а бобины -
4300 об/мин.
Следует отметить, что при дисковом шлифовании скорость резания отличается в различных частях диска - для повышения качества шлифования стремятся работать его периферийной частью. Станки подобного типа используются, как правило, на небольших предприятиях в мелкосерийном производстве.
ТЕЛЕФОН/ФАКС: (495) 267-47-74.
3(26), 2006